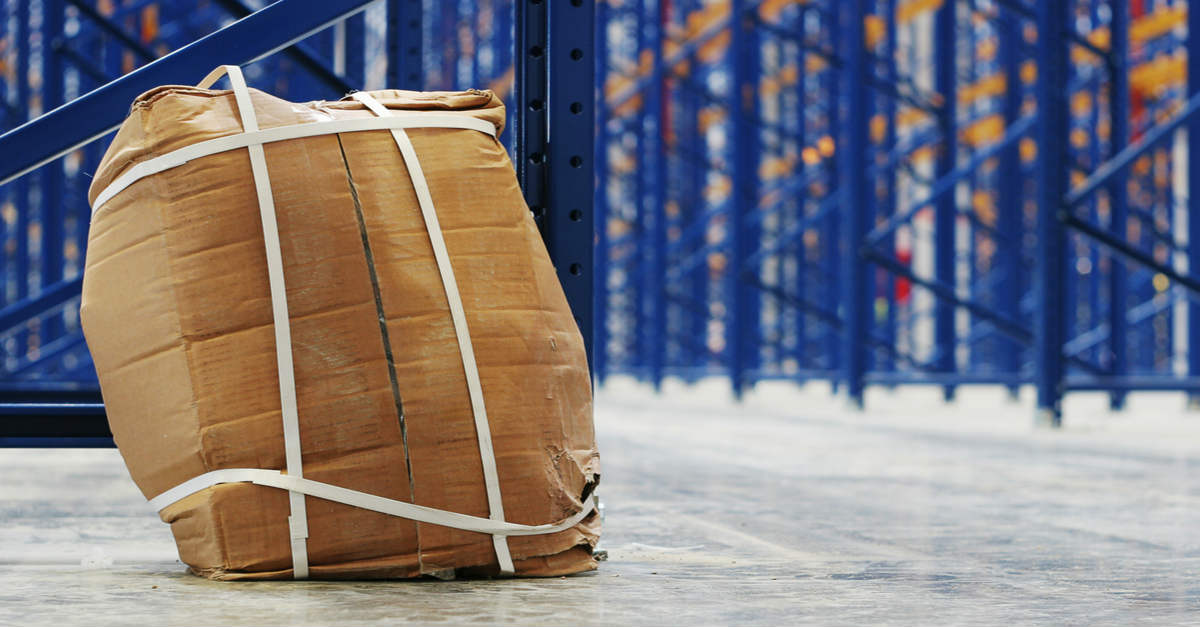
A reader sent me this interesting question:
I would like to better understand AQL usage and more precisely whether inspections based on AQL are effective in situations where the distribution of defects is not homogeneous within the lot.Let’s say the lot is 25,920 pieces split in 36 boxes. From previous observations, most of the pieces in the lot are OK, but a few pieces (200-500) are not OK and they are physically located in a focused part of one or 2 boxes.Is an AQL inspection the right approach in such situations?
That’s a very good question. This reader found a blind spot in the ISO 2859-1 standard (used in what they call “AQL inspections“.
And the reason is simple. The statistics assume that every piece in the batch has the same probability of being defective. If you receive a batch in bulk from a supplier, that’s a fair assumption.
But it isn’t always realistic. Here are a few examples:
- A tool breaks in production, and the next 50 parts are defective. They are not segregated and are shipped together with other parts. They are all concentrated in the same carton box.
- The manufacturer has 5,000 pieces to pack, but finds out that their supplier only shipped enough packing material for 4,900 pieces. They decide to use another material that is nearlythe same. It ends up in the last 2 carton boxes.
- The production manager decides to ship the rejects from a past batch. He places 5 ‘bad’ boxes among the 200 boxes for this shipment.
If you really, really need to catch those cases, you need to do your sampling in a different way (for example, checking a few pieces in each box).
No comments:
Post a Comment