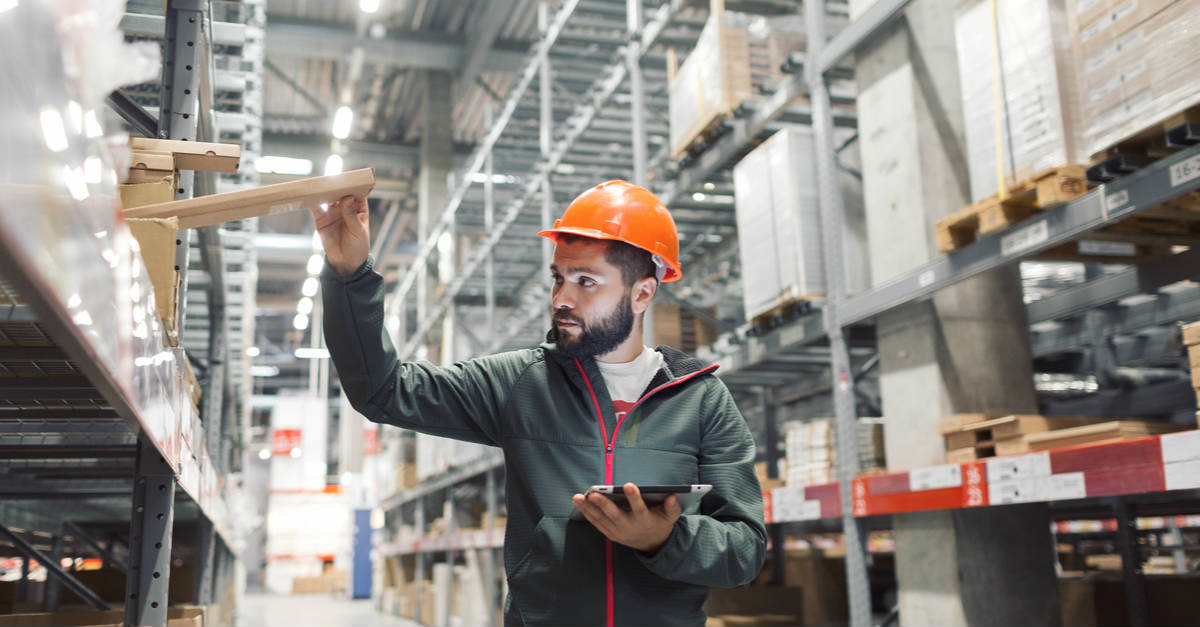
The final random inspection is by far the most popular QC service in China (see my last post, where I listed the other major types of quality inspection services).
It is suitable for nearly all types of consumer goods purchased in Asia. The final inspection report is typically used by the importer to authorize shipment and trigger payment.
When to conduct a final random inspection?
It takes place at the end of production. The whole shipment quantity should be finished and available for sampling. Packing should be nearly (at least 80%) done, so that the cartons can be counted.
If these conditions are respected, the factory cannot hide defective goods in a back room. So timing is of prime importance when it comes to final checking.
I drew a little sketch to represent the key dates to watch closely:
A final random inspection usually takes place in the factory, rather than in the forwarder’s warehouse (or nothing can be repaired). So it is performed before the goods are sent out of the factory.
For urgent shipments, the inspection might occur a few hours before the products are loaded in a truck and then shipped out by air freight. This is not ideal for several reasons:
- The purchaser has no time to study the report and ask questions to the inspection firm or the supplier.
- The inspector only has time to write a non-official report (handwritten and without photos), so misunderstandings can occur.
- In many cases, importers just tell their suppliers “you ship if the QC report is passed” and cannot be reached in time for a decision. This puts a lot of pressure on the factory and the inspector. And what to do if the report is failed? Or if something unexpected is found that might be unacceptable by the buyer?
- If some quality issues are noticed, the factory might not even have a few hours to do a quick repairing!
This is why I always advise to set the final inspection at least 2 days before ex-factory date (e.g. on Monday if the ex-factory date is on Wednesday).
Some importers take more precautions: they ask for final inspections at least 2 weeks before shipment date, to leave room for potential re-work and re-inspections.
What is checked during a final random inspection?
Three types of issues can trigger the failure of the inspection, and potentially the refusal of the shipment by the purchaser:
1. Conformity to specs:
All the relevant aspects of the product are controlled: quantity, components, assembly, aesthetics, function, size, labeling, packaging, etc.
Ideally, the buyer has constituted a document listing all the specifications of the product to inspect, and these specs become the inspector’s checklist. When no such information is provided, the inspector simply collects information for the buyer’s review.
2. Number of visual defects:
Based on the sampling plan, the inspector selects a predefined number of products at random. He checks them one by one, and counts the number of defects, which are compared to the AQL limits.
3. On-site tests:
Depending on the type of products, certain tests are included in the inspector’s job. For example: a product drop test on 3 samples, from 80cm high on concrete floor (if at least 1 sample breaks or does not function any more, the test is failed).
What are the limits of a final random inspection?
Suppliers resent it
Importers often put a lot of pressure on suppliers, who risk a tough re-negotiation of prices (or even an order cancellation) if the products have serious quality problems. QC inspectors are seen as policemen, and might be bribed if supervision is not sufficient.
No 100% guarantee
It is conducted on samples drawn randomly, not on the whole quantity. There is always a small chance that findings are not applicable to the whole shipment, even if the so-called “normal” or “tightened” levels are followed.
Similarly, a dishonest factory can short-ship of switch the products just before shipment (unless the loading of the goods is also monitored).
Too late
If the purchaser only sends inspectors after production is finished, it can be too late. Either because the defective products have to be re-produced, or because re-work takes too long.
This is why I usually advise to conduct an inspection during production, in addition to a final random inspection: problems are caught early, and some suppliers see it as assistance rather than policing.
—-
For further reading: see How Does A Random Quality Inspection Work?
No comments:
Post a Comment