
This article describes the types of quality inspections (before, during, and after production) most widely used in international trade.
They should be performed by 3rd party QC providers (appointed by the buyer), or by the buyer’s own inspectors, if you buy from China, Vietnam, India, or another low-cost country.
What is a quality inspection?
The term “inspection” generally refers to the activity of checking products, whereas “audit” applies to analyzing manufacturing processes and organizations. The quality inspector usually follows a pre-established checklist that is based on the product specifications. Inspected products can be the components used for production, semi-finished goods, or (most often) finished goods before shipment to a customer.
The ISO 2859 standard (derived from MIL-STD 105 E) defines an inspection as an “activity such as measuring, examining, testing or gauging one or more characteristics of a product or service, and comparing the results with specified requirements in order to establish whether conformity is achieved for each characteristic”.
I wrote this article to provide guidance to importers who source finished goods from suppliers.
An important concept: why inspecting earlier is generally better
As a preliminary, I want to emphasize an essential principle of quality management: “the sooner we eliminate errors, the better”.
There are only six ways to deal with defects. They can be either prevented or corrected, and they fall into three broad categories: development, production, and delivery.

The 1:10:100 ratio
Many studies across all industries have demonstrated that there is a cost and time ratio for development:production:delivery of 1:10:100. It means each error will cost 10 times more (in dollars and in time) to fix in production than it would to fix in development, and 100 times more if the error actually reaches the customer.
That’s why checking quality only at the end of production is very risky. But you don’t have to wait until everything is done… As you can see below.
The three most common types of quality inspections
There are mainly three tools at the disposal of buyers, to check on the quality of their suppliers’ products. Each buyer should try to choose the solution(s) that best fit(s) her needs.
Pre-production inspection (a.k.a. “initial production inspection”)
“Garbage in, garbage out”: a factory usually cannot turn defective inputs (components, or raw materials) into good products. And the problems are much harder to detect once the materials are embedded in the final product.
Thus, to decrease quality risks, the inputs can be inspected prior to production. Some samples can be taken randomly and checked visually (or sent to a laboratory for tests). Also, the b
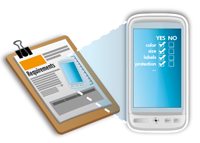
uyer should clearly define what inputs are acceptable, before he gives any order.
An experienced inspector can also examine the making of a prototype/sample, to make sure of two things:
- Has the factory understood the technical files? Do they know what product the client wants?
- Has the development team clearly communicated the requirements to the manufacturing team? Is the equipment for mass production similar to that used for making prototypes?
Usually, production has already started when a pre-production inspection takes place. It allows the inspector to examine the process, and sometimes to check a few finished products. However, in this case, the factory might refuse to stop production (to avoid disruption of the lines), even though the inputs are not conform or the process is not satisfactory.
Generally speaking, pre-production inspections are adapted to customized and complex products. More standard items should be inspected during production (see below).
During production inspection (a.k.a. “in-line” or “in-process” inspection)
Should a buyer wait until the end of production, before doing an inspection? In case products are defective, the following problems might arise:
- The factory has to rework (loss of time).
- If the products cannot be repaired, the factory should re-order components, and re-produce (which means long delays, and a financial loss for the factory).
- The supplier might refuse to repair or re-produce, particularly if the previously-agreed specifications are ambiguous.
Typically, in an in-line inspection, the first products that got out of the line are inspected for conformity. If issues are raised at this stage, the factory can immediately take some corrective actions and avoid delays.
Also, based on the production start date and the number of products already finished, the buyer can have a fair idea about the shipment schedule.
A third advantage of in-line inspections is that the buyer knows where the goods are produced. Some suppliers show a factory to a buyer, and then sub-contract the production in another workshop (this happens every day in China).
Note: some companies make a distinction between inspections performed at the beginning of production and inspections during production. I pasted below an extract of a brochure from the industry leader (SGS) for illustration:
‘Initial Production Check’ permits timely corrections of any non-conformities detected.
‘During Production Check’ allows evaluation of the average product quality during manufacturing.
What it means is that third-party inspectors can either check the first finished products getting out of the line, or come in at a later stage and select samples from a larger pool of finished goods.
In any case, in-process products are rarely checked. It takes a technician to reliably detect errors on unfinished products.
Final random inspection (a.k.a. “pre-shipment inspection”)
This is the most popular type of QC inspection for importers. It takes place once all the products are finished and ready for shipment.
Note: A “packed product” is ready for shipment (i.e. in a closed export carton with full shipping marks). In many cases, the inspector accepts up to 20% of unpacked products per reference. This way, the inspection can often take place without delaying the shipment.
The conformity of the products is checked against a list of criteria defined by the buyer (product quantity, workmanship, function, safety, aspect, size, packing…).
Buyers are advised to ask their inspectors to keep track of which cartons were opened. This way, a 2nd “spot” inspection can give an idea of how seriously the control was performed.
Of the three inspections presented in this article, this is the only one where the total quantity of products can be counted, and where samples of finished products can be drawn in a truly random manner–and thus be representative of the whole batch.
As a result, the results of final inspections are more reliable. And some buyers assume that the inspectors should “guarantee” the quality of the whole order quantity, when the inspection is passed. Unfortunately, it is impossible for several reasons:
- After the inspection is done, and before shipment, many things can happen. A dishonest factory can ship a smaller quantity, substitute the content of the cartons, etc. There is a solution to avoid this: a container-loading supervision.
- An inspection result (pass/fail) is not 100% reliable: even a random sample might be better than the average products; the inspector might make a mistake; an inspector might get bribed by the supplier, etc.
- An inspection fee (around USD300 for one day) is totally out of proportion with the total value of the goods at stake (sometimes over USD100,000).
For further reading on quality inspection, check out what AQL means in simple terms.
No comments:
Post a Comment