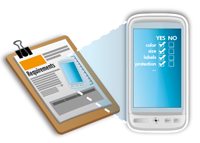
QC inspections don’t ensure quality. They only expose lack of quality. Which is good if you didn’t oversee production and you are about to ship. But it is not sufficient.
Inspecting a production run gives you some information, which can (and should) be used. If you find that the goods can’t be sold, you should find an immediate solution (sorting/rework/reproduction/cancellation) with your supplier.
But some other conclusions can be reached, for longer term improvements.
- If you find some issues that come from a product design mistake, you should take the appropriate corrective measures on your side.
- If the goods are not conform to your requirements, it might mean the factory’s quality system has holes. Improving their quality system can be a long and arduous route, but it can also be the most beneficial in the long run:
- Audit the quality system to find these holes
- Write a procedure to cover these holes
- Train the workers to follow the procedure
- Audit the workers to verify whether they follow the procedure
What kind of factory can accept this type of involvement from the buyer? In China, not many. If you find a 100-operators manufacturer and if your orders represent half their annual capacity, it might be applicable. Especially if the owner is relatively open-minded, and very motivated.
Once you get a factory up to a higher standard, it can be very gratifying, but it might only last for 2-3 years. They might double in size every year, and reach a point where your orders don’t mean much to them any more…
Unfortunately, it is a continuous cycle. Find a promising factory, invest time and energy into them, see the progress they make, reap the fruits from that cooperation, and then start over with another one.
No comments:
Post a Comment