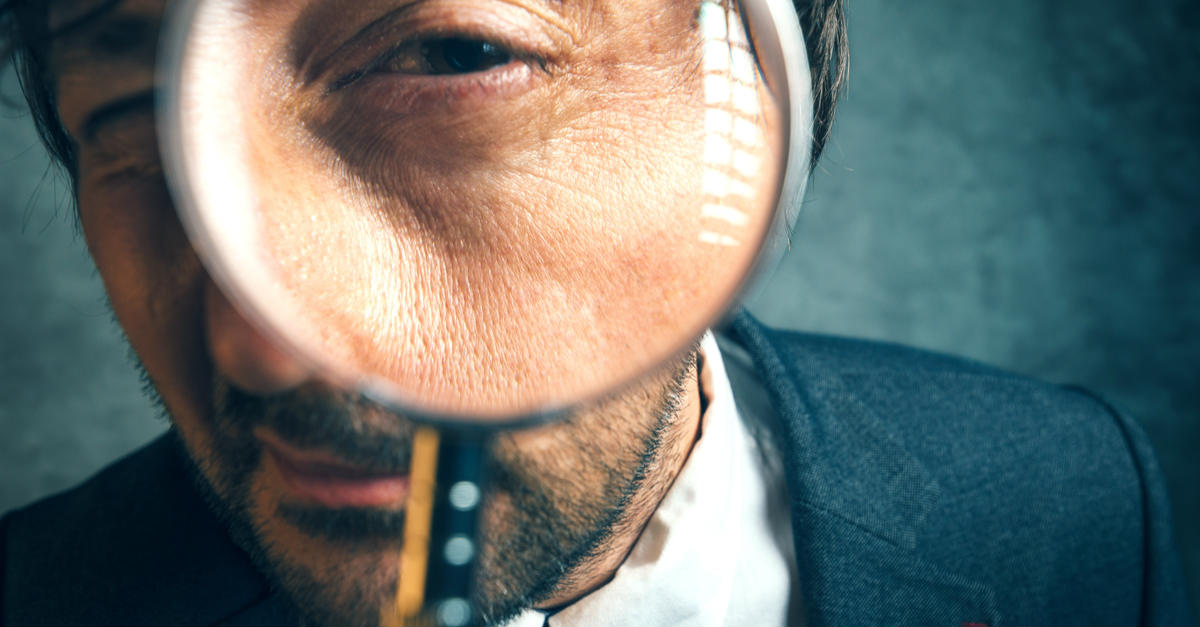
Four types of quality inspection services are usually distinguished. Each one corresponds to a particular step in the production process. They are all part of the toolbox of every importer, when it comes to buying in China and other low-cost Asian countries.
I tried to summarize the options available to buyers, in a visual manner.
The four types of quality inspection services:
All quality inspection services are not adapted to the same situation:
1. A pre-production inspection tells the buyer which kind of raw materials (or components) will be used. Factories are often suspected of lowering their costs by purchasing substandard materials, and this can be disastrous for the buyer (e.g. the wrong kind of chip in an electronic device).
The pre-production inspection can also focus on the processes followed as production starts. Sometimes this can also be critical, as Chinese factories very often cut corners and do not respect the buyer’s blueprints (e.g. patterns for cutting fabric are received from the buyer, and they are modified to make the process easier and faster).
2. A during production inspection (often called “DUPRO” in the industry) allows the buyer to have an idea of average product quality, early in the production cycle. It is the most useful and the most under-rated tool at the disposal of importers, who often only rely on final inspections.
It usually takes place once some finished products have come out of the lines. If quality issues are found, what is already produced might be re-workable, and corrective actions can be taken for the rest of the job. It gives buyers the time to plan ahead, and even to avoid delays (repairs and re-inspections take much more time when problems are noticed after all production is finished).
3. The final random inspection (also called “pre-shipment inspection”) is by far the most common type of QC check. It takes place once 100% of shipment quantity is finished and at least 80% is packed, so it can be a real random inspection (this is not exactly the case if quality is checked earlier earlier) and suppliers cannot play games.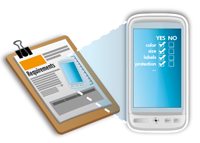
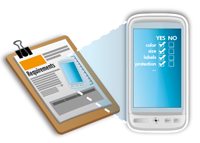
It puts pressure on suppliers and gives power to buyers. Its objective is really to confirm a shipment’s quality, rather than catching issues early. Therefore I usually advise my clients to complement final inspections with a DUPRO, to avoid finding disasters at the last minute.
4. The container loading inspection, like the pre-production inspection, it is seldom used. But it can be a worthwhile option in some specific cases.
It can be useful if the buyer has a precise loading plan and needs it to be respected very precisely (e.g. some cartons are too fragile to be placed at the bottom), or if the packaging is not conventional (e.g. some garments hung on bars, with no carton protection).
It can also ensure that the right kind of products are shipped out in the right quantity, when the importer places no trust in his supplier or when several suppliers bring their products for consolidation.
Only the most sensitive projects require all four types of inspection. Generally, only one or two of these tools are used, depending on the risks identified by the buyer.
These quality inspection services are used mostly for consumer goods involving little customization. Different approaches are often chosen for ensuring that industrial products are up to specs (much more attention is spent during development and early production).
—
Related posts:
No comments:
Post a Comment