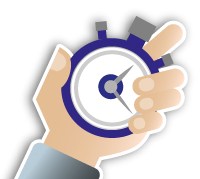
The quality assurance programs of most importers, when it comes to their China purchases, are far from being fool-proof.
As Richard Brubaker wrote (in “20 Things I Have Learned About China”):
There is no “Poorly Made in China”. There is only poorly understood, badly planned, and horribly managed.
And I found an excellent illustration of this principle: a newspaper article about tainted children jewelry that points out the holes in quality assurance programs:
So far this year, 20 different children’s jewelry items have been recalled in Canada for being packed with lead, nowhere near the maximum allowable limit of 0.06 per cent.
Health Canada product safety officers test suspicious products that they find in stores, but most faulty jewels are probably sold without being tested.
Without a government-mandated testing and certification program requiring manufacturers, importers or private labellers to test children’s products at accredited laboratories prior to stocking store shelves, it’s up to the private sector to run its own quality assurance system.
The problem is, this system is generally not adapted to the tactics of some Chinese suppliers.
What does the importer say, to his defense?
Montreal-based Dollarama Inc. knows which factory in China is responsible for making the Valentine charm bracelet sold exclusively at the discount chain that was recalled in the spring after Health Canada tests showed the item contained 92 per cent lead.“It’s a simple human error in the sense that without talking the exact details, there’s a process in place under which we have quality controls and we do inspect the factories and we sample products. And in this case, there’s been a mistake at this stage of sampling the product”
What does the supplier say, to his defense?
Hong Kong-based Betawin Enterprises, when pressed by Canwest News Service, implied a subcontractor may have made the goods instead of its own “mainland bureau” — a small factory on the third floor of Tower C, Area A in the Longquan Technological and Industrial Park, an industrial park just outside Shenzhen, China’s city centre, where about 60 workers make cheap jewelry for minimum wage, $142 a month.“As you know, we are a trading company. We placed the order to the factory to produce the goods and we would ask the approval samples for testing and quality before shipment released always. During the process, everything was OK and we hadn’t found any problem. But we fall into a trap and we believed that the maker was dishonest to ship us the goods with different materials between the approval sample and shipment.”
What did the manufacturer probably do?
Midler, based in Hong Kong and a frequent visitor to Chinese factories as a troubleshooter for companies that source their products in China, says it’s not unusual for factories to be responsible for choosing the sample sent to be tested. This means a manufacturer can make a substandard product while providing an acceptable sample for testing.
Another issue, in other cases, is that many factories provide a fake test report. This is very, very common. Especially in the Guangdong and Zhejiang provinces, where exporters are particularly savvy.
What should the importer have done?
- The importer should have sent an inspector in the factory to check the workmanship, but also to pick up some samples and send them to a testing laboratory.
- The lab should be chosen by the importer, and provide all test results directly to them.
- And the importer should insist to customize the products in a certain way, to make it impossible for the factory to switch them, i.e. to make good products and ship them to another buyer (and ship substandard goods to this importer).
————————–
For further reading:
No comments:
Post a Comment