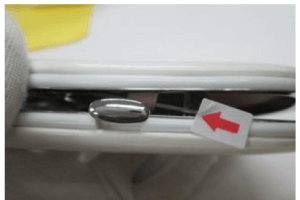
Within the inspection standards the buyer should clearly define the classification of defects for quality control in China to ensure a clear understanding of the expected quality from the supplier and the QC standard to which the inspector will inspect. The classification of defects should be applied by all parts and communicated prior to the production. This article defines the standard defect classification system used for inspections in China.
Inspection standards based on ISO 2859 and AQL level II (0, 2.5, 4)
The inspection standard used by most of the inspection companies for quality control inspections in China and Asia is the “AQL level II (0, 2.5, 4)”. It defines the sample size, the quality limits for quality control in China.
Classification of defects for quality control in China
Once the framework is defined, the next step is to classify the defects. Most buyers separate defects into three types based on the standard definition commonly used by third party inspection companies as follows (here are more examples):
- A critical defect is likely to result in hazardous or unsafe conditions for individuals using or maintaining the product.
- A major defect is one, other than critical, that is likely to result in failure, or to reduce the usability of the unit of product for its intended purpose.
- A minor defect is not likely to reduce the usability of the product for its intended purpose.
Buyers can change the definition of critical, major and minor defects based on its own requirement and quality expectations. In this case, it is necessary to inform the supplier and the inspection company at the order confirmation.
And you: do you determine your own classification of defects for quality control in China?
No comments:
Post a Comment