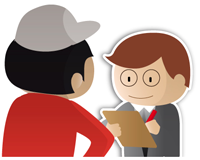
A few months ago, we illustrated how random inspections work, and we got very positive feedback.
This time we designed an infographic about the way a factory audit works in China and other low-cost Asian countries:
We tried to put factory audits back into the wider context of the sourcing process. What do you think?
>> Related eBook: How to Evaluate the Costs of Quality in a Factory
——————-
TRANSCRIPT:
How are factories audited in China?
Approving the factory where production will take place is the last step in the process of selecting a supplier. Its objective is to confirm that the factory can deliver the right product in the right timeframe.
Regular audits of a given factory can also encourage progress over time by pointing to areas of improvement.
Factory audits are the last step in the sourcing process
A factory audit usually takes place after a group of potential suppliers have been screened down to a few serious candidates. It is the most expensive and the most in-depth form of supplier evaluation.
It is important to get the factory to confirm the availability of key managers on the desired date. Surprise audits are reserved to certain situations only.
Documents verification
The auditor does not only ask for basic financial information. He requests the factory’s official licenses and certifications, and looks for evidence of other customer orders.
Note: ISO9000 certifications do not mean much in China. Hence the need for in-depth investigation (see below).
Observation of the production area
The auditor should describe the main types of products seen on the lines, and the production organization (including facilities, equipment, workers, and product flows).
Here are the key questions to answer:
• Is this factory capable of making the buyer’s products?
• Does this factory focus on low cost, or can it handle complex workmanship?
• What is the rough capacity (in number of pieces per week) for the buyer’s products?
Verification of the quality system
The auditor follows a checklist loosely based on ISO9000 series. He typically observes the verifications of incoming materials, in-process products, and finished goods. The objective is to look for holes in the factory’s quality system, and to evaluate their reliability.
Every claim by the factory has to be supported by written records.
Social compliance issues
The auditor checks whether the factory respects its country’s regulations, and some other criteria from a standard such as SA 8000 or ISO 26000. Verifications focus on pay records, worker interviews, observations in the workshop, etc.
This is often conducted as a separate audit. The objective is usually to avoid public relations risks for the importer or the retailer.
Report preparation
The auditor prepares his report, based on his observations and his subjective evaluation.
Caution: factory audits tend to follow a scientific approach, which favors larger manufacturers… who tend to pay no attention to small orders. Therefore, audits are dangerous if the pre-qualification phase was not oriented toward suppliers of a suitable size.
No comments:
Post a Comment