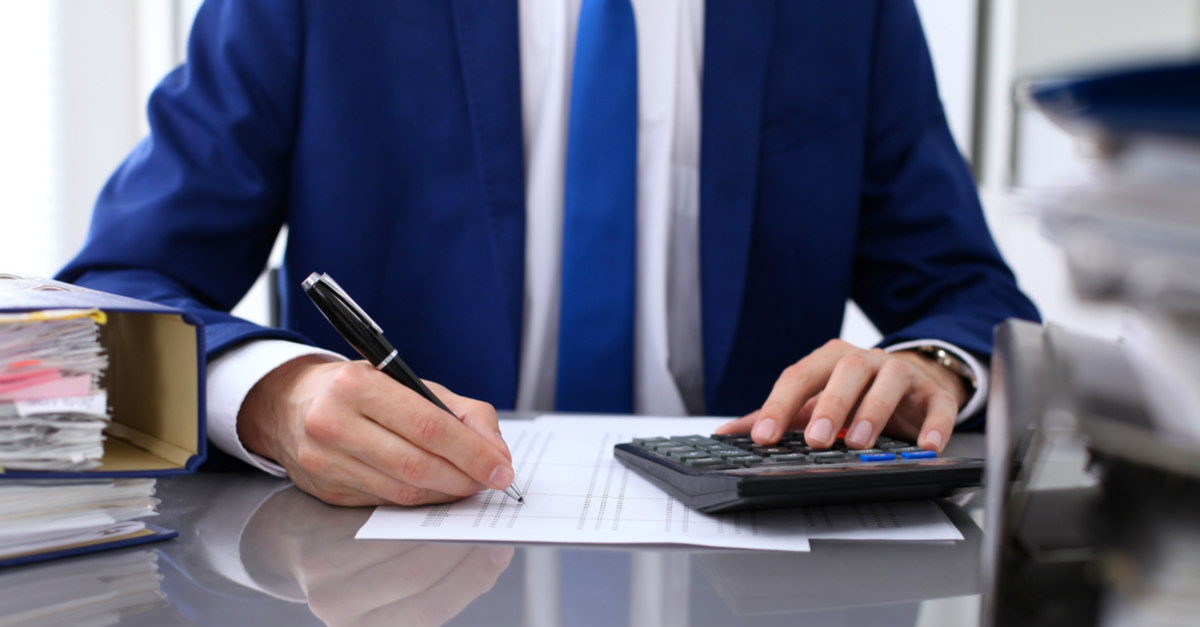
A quality control plan is the document that lists all the quality-related checkpoints to be passed during/after a production run. Depending on the situation, it can include process, product, or legal checkpoints. Getting this document approved is an essential step before production is allowed to start.
There are two types of quality control plans:
- The product quality control plan to include in a contract with a Chinese supplier
- The process control plan that decomposes production in each process step (often called control plan)
1. The product quality control plan to include in a contract with a Chinese supplier
Defining a basic quality control plan with every new supplier is one of those things that take little time but that can save lots of time and money. It can be standardized and sent to every supplier with only minor adaptations. Buyers are advised to talk about it with a manager working for the supplier company, and to get it signed/chopped.
A quality control plan is a standard exhibit in contracts drafted by specialized lawyers, together with the purchase order and the product specifications.
So, what to include in a quality control plan?
Of course, it depends on each buyer’s needs. I wrote a short (and fictitious) plan below, for inspiration (A is the buyer and B is the supplier).
Timing of inspections
A reserves the right to send one of his employees/representatives in the factory to inspect production at anytime.
Communication of status of production
B should send an email to A 3 days before it receives the main materials/components, and should send a confirmation email on the day they arrive in the factory’s warehouse.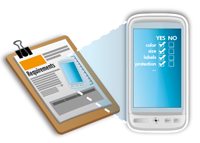
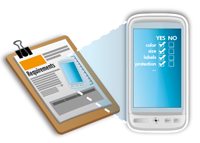
B should send an email to A 3 days before the factory starts working on its order, and should send a confirmation email on the same day it happens.
B should send an email to A 3 days before the first finished products are out of the lines (i.e. fully produced), and should send a confirmation email on the same day it happens.
B should send an email to A 3 days before 100% of the shipment quantity is finished and 80% is fully packed (i.e. ready to ship), and should send a confirmation email on the same day it happens.
B should sent an email to A every time some samples are sent to a laboratory for testing.
Description of quality control activities
A reserves the right to perform the following quality control activities, and any other activity not described below.
Product inspections: random inspections of products, conducted based on the ISO2859-1 standard (single stage, normal severity, level to be determined as we see fit). Acceptance quality limit (AQL) is 0% for critical defects, 2.5% for major defects, 4.0% for minor defects.
Lab tests: B will have to send 2 samples to ABC laboratory for XYZ tests, in order to respect the consumer safety law of the importing country. These samples must be extracted from bulk production. A may, or may not, ask the inspector to pick these samples.
Testing equipment that must be available in the factory
For your own quality control activities, and for our inspection activities, the following pieces of equipment must be present in the factory:
- Weighing scale for export cartons
- Weighing scale for the products
- Hi-pot tester
[Customize this list as you see fit. This information should be listed in your product specification sheet or QC checklist.]
What to do in case of failure?
If a product inspection or a laboratory test is failed, B will get in contact with A within 24 hours with a detailed explanation. If shipment is delayed because of unacceptable quality, B will bear all consequences for this delay.
If a product inspection is refused, A has the right to ask for a re-inspection, the cost of which will be re-invoiced to B in full. And so on until the inspection accepted by A.
If some products are found defective and/or not conform to product specifications, B will check the whole quantity and will sort them out of bulk quantity. If re-production is impossible, B should let A know immediately about it.
If the inspection is failed (and refused by A) twice in a row, A reserves the right to ask B to pay for a third-party inspection firm (appointed by A in written), which will do a 100% check on the shipment.
If a lab test is failed, B will have to pay for additional tests from the same laboratory.
What inspections and lab tests do NOT represent
Product inspections and lab tests are only tools used by A to take a decision. Putting pressure on an inspector is useless and is forbidden. Trying to give money/favors to an inspector is forbidden by law and will end all business relationships between A and B.
Even if all inspections and tests are passed, B should wait for A’s agreement for shipment.
Even if all inspections and tests are passed, they do not relieve B from its contractual liabilities or prejudice A’ right for compensation for any apparent and/or hidden defects not detected by the inspection(s) and/or the test(s).
2. The process control plan that decomposes production in each process step
Writing this document forces the manufacturer to do two things:
- Identify each process step, and indicate whether it is critical (i.e. likely to cause serious quality issues if improperly handled) or not;
- Define the process controls: what to check, how often, using what methods, and what to do if issues are found.
Here is an example of process control plan:
In this example, you can see what to check regularly on a die casting machine. (Note that the mould and the materials also need to be checked regularly — it’s not only about the machine.)
It is mostly used by the North American and European auto industry, but it is VERY useful for any production. The more immature and/or complex the process, the more useful. We seldom see it for a very simply production (e.g. kitting together 2 components by hand.)
Ideally, this is prepared by the manufacturer. But sometimes the buyer has to send their own engineers or bring in external resources. (We routinely prepare control plans together with the work instructions for production operators, in case the manufacturer is not motivated/capable of preparing those documents.)
Note that the control plan often includes a mix of process controls and product controls.
Here is an example of product control:
What types of product controls are often included?
- Incoming component checks
- Semi-finished product checks
- Finished product checks
———-
For buyers of standard (off-the-shelf) goods to be made in China, I would advise to first spend time on defining your requirements concerning the finished products (by following the guidelines in this article). It includes the types of defects you expect as well as their severity.
No comments:
Post a Comment