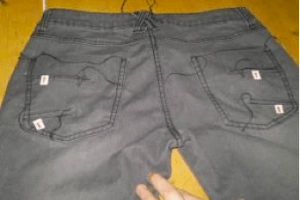
How to inspect the quality of garments?
At AQF, we try to treat garments as a separate product category, and we advise our clients to follow a certain sequence of quality inspections:
First, an FAI (First Article Inspection)
The goal is the catch quality issues as early as possible, by checking the first finished products getting off the lines.
Advantages:
- Most of the serious issues can be noticed during an FAI.
- If problems are noticed at this stage, the client can ask the factory to set up corrective actions, and then resend an inspector a few days later to perform a DPI (more about DPIs below).
Drawbacks:
If the inspector comes when 200 pieces are finished, there are certain risks:
- More than 90% of garment factories are poorly managed. They might announce that 200 samples will be finished, and actually nothing is completed when the inspector comes.
- Some issues can appear later in production, or on sewing lines that have not started yet.
- It is not possible to have an accurate opinion about average quality. The first products out of the lines are the worst ones in the whole batch. On the other hand, the factory knows an inspector is coming, and it is easy for them to check the products more carefully.
However we believe that, in 80% of cases, it is a very good idea to do an FAI.
In case some measurement issues are noticed during an FAI or a DPI, the importer should receive samples that are representative of these issues, in order to check the fitting. There is enough time to wait for the samples before taking a decision.
Then, if applicable, a DPI (During Production Inspection)
The goal is to check some samples taken at random, once 20-50% of the order quantity is finished. DPIs are not used very often for garments (except in case of an FAI that failed, to check the improvements).
The major benefit of a DPI is to get a good idea about the average quality of the products, before all is completed.
Finally, a PSI (Pre-Shipment Inspection)
The goal is to draw a representative sample and to get a precise idea about the total order, before it is shipped out.
Advantage:
- It is the only type of inspection that allows us to confirm the average quality of a batch (if the factory actually shows the inspector the quantity requested in the QC plan).
- The inspector can check the labeling and packaging, and also count the quantity precisely.
Example of a PSI on garments:
Rather than describing inspections from 10,000 feet high, let’s take an example: an order of 3,000 pairs of jeans, in 12 sizes / 2 colors / 30 measurement points, under level II.
Here is how we would check it:
- We would draw 125 samples for visual defects (not for measurements)
- For measurements: in this situation, we can check 1 sample per size and per color (i.e. we check measurements on 24 samples) and keep the workload at 1 man-day.
If the client requires measurements checks on more samples, there are 2 options:
- Remove some measurement points (are they all necessary?)
- Send more than 1 inspector, based on the number of pieces the client wants us to check.
No comments:
Post a Comment