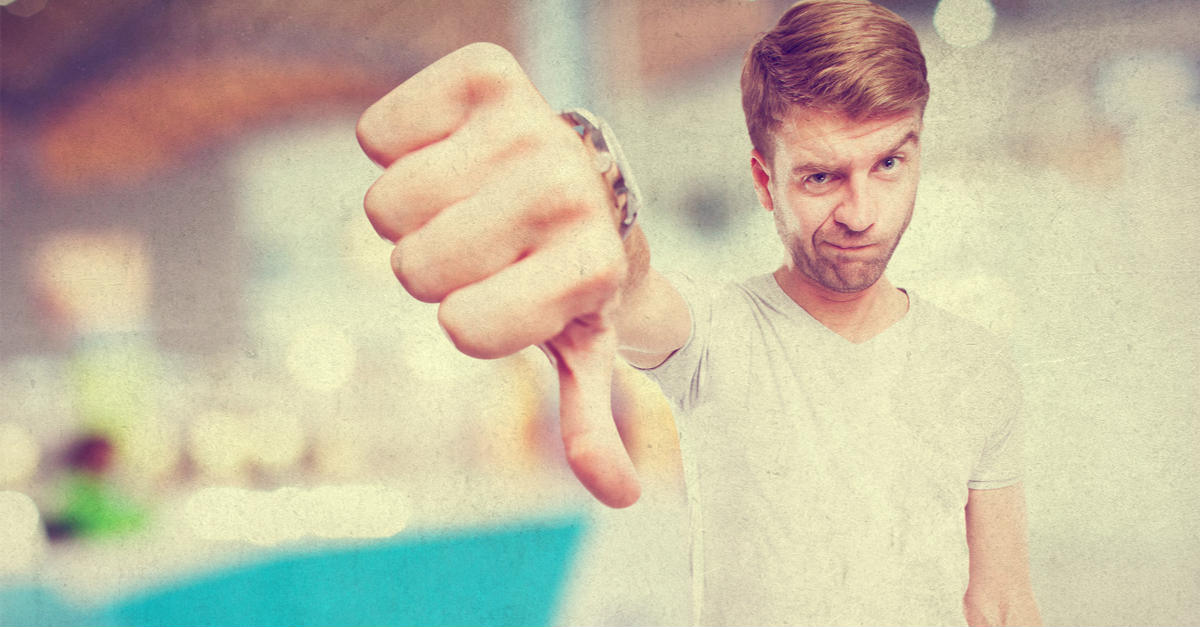
The sad truth in China is, 5% of the manufacturers are doing a good job consistently, and the rest have ups & downs that irritate and frighten Western customers.
And, of those 5% that do a good job consistently, 0.5% do so because of good systems and the other 4.5% do so because operations are not very complex and management watches what happens carefully.
Yes, I made these numbers up. But that’s my impression after 12 years spent working here across multiple sectors (from apparel to tier-1 automotive, and from furniture to electronics). Bad suppliers quality is still a real problem in China.
But why can’t these manufacturers even STOP BAD QUALITY? Because of a series of issues in the quality systems.
Typical gaps in the quality systems of Chinese factories
We drew this simple infographic to illustrate the issues we have seen most often.
Does it sound familiar?
- Inconsistent product quality from suppliers, which causes delays and other production issues
- When inspectors do check production, they write findings on paper, and data integrity is a serious concern
- QC is only the responsibility of the QC department, and the production staff’s performance is evaluated on the basis of quantity shipped.
- The managers think “to ship fewer defective units, we need more inspectors to take the bad pieces out and it costs more”, rather than working on process controls and preventive maintenance.
- Manpower and materials are wasted in rework and scrap.
- Data analysis is quite difficult. It requires a lot of data entry, and is ready days after an issue has appeared.
- No systematic feedback to the previous process, or to external suppliers.
- Not all issues are caught. Customers are never sure their standard will be respected.
Is this what you see in your suppliers’ factories?
No comments:
Post a Comment