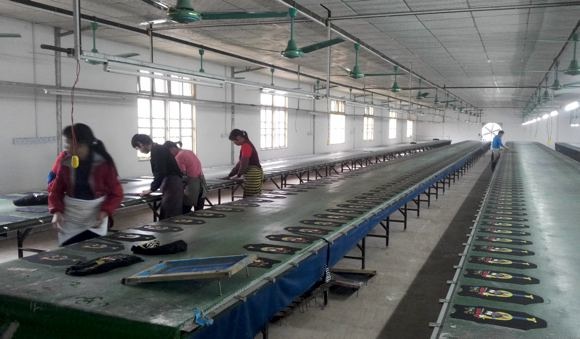
Most importers, when they visit their supplier’s factories, only see the final operations. However, in China, many problems come from the sub-suppliers. Here is an example.
Photo of the workshop where rubber print is applied (the cut pieces are lined up, and then colors are applied one by one):
We work with a purchaser of baby garments. The supply chain looks like this:
- The yarn is knitted, and the fabric is dyed by a dyeing mill,
- Accessories (snaps, zippers, bags, cartons…) are purchased from other sub-suppliers,
- Fabric is cut by the sewing factory,
- Some cut pieces are sent to a printing factory (see below photos) for applying the rubber print,
- The garments are sewn in the sewing factory, and finally shipped out.
We went to see the printing factory, because we noticed frequent problems of imprecisions in the prints. You can see the way prints are applied on the cut pieces in the photos below.
Photo of the way they apply the rubber print in white color:
Photo of the frame for applying the white color:
The advantage of visiting this sub-supplier was to show him what needs to be improved. They immediately applied the corrective actions.
For example, some yellow color was missing. They added it manually, with the help of toothpicks.
Photo of the way they add some missing yellow color (blurred for confidentiality purposes):
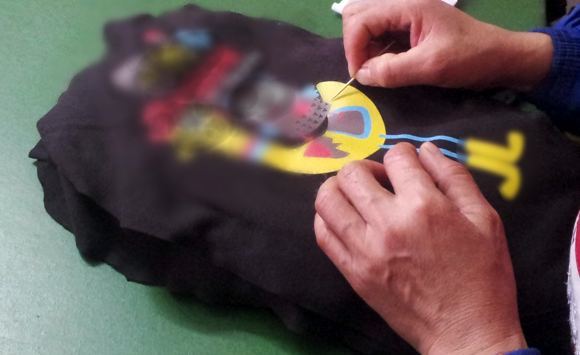
Photo of the way they enlarge the area where the yellow color is applied:
Bottom line:
- If you can (and your suppliers are transparent), go and see the sub-suppliers. You will show them what your quality standard is, and you will learn how they are organized.
- If an operation is highly sensitive, yet is performed by a sub-supplier, you must know who the sub-supplier is and then pay him visits.
What do you think?
No comments:
Post a Comment