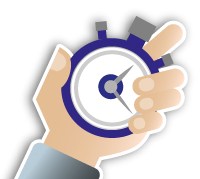
I have been to Chinese factories a few times for solving problems. In one case, the factory pretended the goods really couldn’t be made as intended by the importer (that was true). In another case, the QC inspector found many defective goods that seemed to come from the same issue, production was still running, and the manufacturer was incapable of finding a solution.
I recently read about the steps usually followed in the Toyota group for solving a problem, and I think it is a very valuable approach. Make sure you come back to this page when you have some on-the-ground troubleshooting to do!
1. Identify the problem
What is causing a problem? How bad is it? What are the consequences (delays, scrap, poor quality…)?
The problem is certainly hurting the manufacturer financially in one way or another. Remind them about it, to get some buy-in on their side. You’ll need their patience as you go through the next steps.
2. Clarify the problem
Go on site and see what happens:
- First, make sure you know what should be happening if all were running fine
- Second, see what is actually happening, and identify what goes wrong
- Look for the point of cause, and observe it
It is important to be disciplined and to follow this process. Looking for the point of cause (i.e. where things go wrong and cause the problem) can take hours, but it s time well spent.
3. Investigate causes
- What is the direct cause of the problem?
- Launch a 5-why investigation, until you get to a cause that, if addressed, will prevent recurrence of the problem.
Spend time until you full understand what is going on. Get the factory technicians’ suggestions, but only after you have observed the process first hand.
Again, most of the factory’s employees will try to come up with solutions, and will be tempted to skip this step. It is a mistake. Solutions are obvious if you are very familiar with a problem, so spend time to understand the situation first.
4. Test countermeasures
- Address the root cause, by changing only one factor at a time (to keep cause & effect relationships clear)
- Test new approaches until the problem stops
This is the time to implement solutions and to test them. Again, if you have followed the first 3 steps meticulously, this should be easy and obvious.
5. Follow up
- Confirm the problem is solved for good
- Make the countermeasure part of the standard operating procedure
If the manufacturer is not well organized, chances are that you will have to train the operators (not just in the day shift!) to do their job correctly. Troubleshooting is done, but is never really over in China…
No comments:
Post a Comment