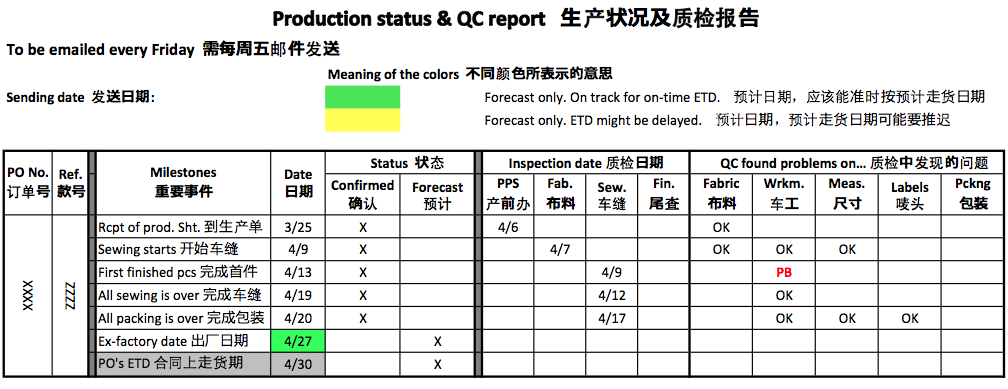
We provide more and more training sessions for inspectors of factories and trading companies. I don’t know anybody else who provides this service in China, but I think it responds to an enormous need.
The training can be about the product itself (what to check, how to check it…). Or, if we focus on an inspector who has already been working for a while in that factory, the training only covers the reporting & auditing system. The objective is to avoid their natural tendencies (see Chinese-style quality assurance).
Adaptations to each situation
There is no such thing as a generic training, when it is done “on the job”. It is necessary to adapt the content of the training to the client’s organization.
I do this by asking a few questions, sending a proposal that goes into the details of the system to put in place, and then incorporating the client’s feedback.
For example, am I going to train a factory employee? An employee of a trading company? An employee from the buying organization? They don’t have the same involvement in production, and they don’t have access to the same information (product specs, PO number, target shipment date…).
Another example: will the inspector(s) check every step of production? Or is it not realistic, and the one inspector should concentrate his efforts on final inspections?
Setting up a QC procedure
The training is based on a procedure that includes:
- Identification of the pieces that were checked (with small sticker in a non-prominent place, for example)
- Filling out a simple QC report (based on the AQL) after each inspection
- Keeping the QC reports in a registry, and communicating their results regularly to the client
This way, it is easy to perform unannounced audits of the inspector, and to help him improve his performance over time.
Then, an instructor spends a few days with the inspector, to make sure the procedure is understood and respected. Good habits must be taken immediately… Or they are forgotten!
Simple QC reporting
The basic principle is: if the paperwork is too time-consuming or too complex, the procedure will not be respected.
Here is an example that we prepared for the inspector of a trading company, in a garment factory. The “milestones” are the main production & shipment steps.
The inspector didn’t know English, so we prepared a bilingual form. We can easily see the inspection date, what was checked, and whether there was a problem.
Once a week, the inspector copies and pastes these data into a more comprehensive form, and emails it to the client:
Anybody has experiences in this field and can provide suggestions?
No comments:
Post a Comment