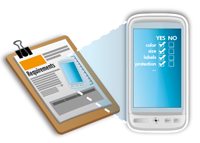
I am often asked questions such as “what is the difference between audits and inspections” or “why are lab tests necessary if you send an inspector”. In this article I will show how these three types of services fit together.
Let’s start with the service that is needed even before a purchase order is issued.
1. Factory audits
Auditors usually check a factory for capacity and reliability. They verify:
- The facilities and equipment (can they make this product, and do they have the capacity to complete an order in a reasonable amount of time?)
- The system (are there any dangerous practices? e.g. they never check the components from their suppliers.)
- Basic information such as the size, the main products, etc. (did their salespeople tell their truth?)
For more details, see this infographic.
I always recommend a factory audit to importers who are about to work with a Chinese supplier. I could cite many cases where the buyer decided not to work with a supplier after seeing an audit report.
Weaknesses of audits
A factory might have perfect systems, workforce, and machines, but they might decide to cheat their customers. It often happens in China. Here are a few examples:
- They may decide to subcontract production to another manufacturer that was not audited. That’s how Walmart Canada learned that their products were being made in the Tazreen factory that burned in 2012.
- They may decide to use cheaper components that are not conform to the buyer’s requirements. That’s how Mattel found out that many of their toys were covered in lead paint, back in 2007.
- They may alter their formal process, for example not maintaining storage temperature for food products.
A skilled auditor will spot some of these cases, especially if he conducts a process audit.
Unfortunately, auditing agencies in Asia typically hire auditors with no process knowledge. They see their job as verifying conformance to a checklist derived from a standard (ISO9001 for quality, ISO14001 for environment protection, and so on), and they focus on documents more than “real world” issues.
That’s why checking how each batch is made is important — that’s what inspections are used for.
2. Product inspections
Inspectors check the products for conformity to requirements. Inspections come into play more “down the pipe”. They check the results of the systems and processes that auditors check.
For most consumer goods, an inspection is usually composed of four steps (I am grossly simplifying):
- Evaluating the quantity of goods, and picking samples
- Checking the products against the client’s specifications and/or perfect sample
- Looking for visual defects on all picked samples
- Performing tests on a few samples
For more details, see this infographic.
There are very few cases where a product inspection is not necessary. If you purchase from China without checking your products (or appointing professionals to do it), you are taking serious risks. Once the products are shipped out and the order paid in full, buyers have no recourse.
Weaknesses of inspections:
- When there are many different types of products (e.g. 20 types of valves, with 2,000 pcs per type, for a total of 40,000 pcs), performing an inspection on samples that are picked among each type of product is very expensive. It multiplies the time to spend on site, so that many man-days of work are needed.
- Once production is finished, finding problems is very important — it avoids a very bad surprise to the buyer — but it does not solve the problems. That’s why, in many cases, inspections during production make sense. It acts as an early warning signal and allows the manufacturer to make adjustments while it is still possible.
- Inspections typically take place in the factory or in a warehouse. In 99% of cases, the inspector comes to the products, not vice versa. It creates an obvious problem: the products often need to be tested, but some of those tests require devices/instruments that cannot be brought by the inspector. That’s why samples are often picked and sent to a testing laboratory.
Which brings us to the next part…
3. Laboratory testing
In a serious lab, a trained technician will respect exactly the right procedure (preparation in the right conditions, testing with properly-calibrated equipment…). However, laboratory tests are typically done on a few samples only — while hundreds of samples can theoretically be checked during an inspection.
Here are a couple of things to keep in mind when it comes to lab testing:
- As the buyer, you need to choose the testing laboratory. If a supplier tells you “here are certificates/test reports corresponding to a previous batch” or “we can take care of the testing with a local laboratory which is fully accredited”, be careful. They are offering solutions that carry maximum risk for you. Buying a certificate from any lab is possible in China. And many ISO 17025 certified labs routinely give passed report without performing any test.
- It is crucial that the samples picked for testing come from bulk production. Smart suppliers prepare a few nice samples that will pass the tests. To avoid this risk, send an inspector during production and ask her to pick samples and to send them to the lab of your choice.
I wrote the sequence to follow in this article.
Is something still unclear?
No comments:
Post a Comment