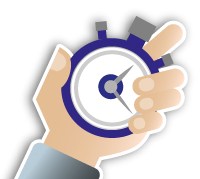
Today we are focusing on the way to audit a rubber molding process. It is quite common in tire factories, but also in many other productions.
What are the Rubber Molding Processes?
Processing rubber to produce final products for end use really depends on what the shape and product is. The main processes for shaping rubber are Extrusion, Compression Molding, Transfer Molding, and Injection Molding.
Tires are the principal product of the rubber industry; tires are about 75% of total rubber tonnage.
Other important products:
- Footwear
- Seals
- Shock-absorbing parts
- Conveyor belts
- Hose
- Foamed rubber products
- Sports equipment
1. Extrusion
Extrusion is a continuous manufacturing process in which rubber is squeezed through a die and then vulcanized (industry terminology for cured). The die gives the extrudate its shape. The required pressure is produced via a conveying screw, in which the material is mixed, compressed and extruded through the die form to produce the final shape.
Extrusion Process Steps
- The extrusion process begins with the unvulcanized (uncured) rubber compound being fed into the extruder.
- Next, the flutes of the revolving screw will carry the rubber forward into the die, with an increase in pressure and temperature occurring as the material gets closer to the die itself.
- Once it reaches the die, the built up pressure forces the material through the openings, where it will consequently swell in various degrees based on the material compound and hardness.
- Because rubber has this tendency to swelling, many extruded parts require compensation on the cross sections of the die.
- During the vulcanization (curing period), the extruded rubber will swell or shrink in both its cross section and its length depending on the type of rubber compound used.
2. Compression Molding
Compression molding is a process that involves taking a rubber compound or mixed raw material and creating “preforms” in the basic shape of the end product. The preforms provide a surplus of material to be placed in the cavity, thus ensuring a total cavity fill. Once in place, the mold is then closed, applying both heat and pressure to the preform and allowing it to fill the cavity. When the cavity is filled, excess preform material spills out into overflow grooves. Following this step the rubber is then demolded, usually by hand, leaving us with the molded rubber product.
Compression Molding Process Steps
- Uncured rubber is preformed into a control weight, shape and specification.
- Rubber preform is then placed into the mold cavity.
- Rubber mold is then closed compressing the rubber to fill the molds cavities.
- The mold remains closed under pressure and held at a temperature to allow the rubber to reach optimal cure.
- Compressed rubber parts are then removed from the mold and the process is ready to begin again.
3. Transfer Molding
As with compression molding, transfer molding requires secondary raw material preparation into preforms. It differs, however, in the placement of these pre-forms into a “pot” located between the top plate and a plunger. When the preforms are placed into the pot, the mold is then closed and the material is compressed by the plunger and transferred through a sprue system into the cavities below.
Transfer Molding Process Steps
- Uncured rubber is preformed to control weight, shape and specification.
- Rubber preform is then placed into the pot.
- The ram then distributes the rubber through the runner and gate system into the cavities.
- The mold remains closed under pressure and held at a temperature to allow the rubber to reach optimal cure.
- Parts are then removed from the mold and the process is ready to begin again.
4. Injection Molding
Injection molding of rubber is based upon a process intended for the molding of plastics. Rubber injection molding successfully alters the plastics process by heating the rubber and placing it under significantly more pressure per square inch of cavity surface in molding. This is different from the plastic injection molding process where the materials are cooled under less pressure. Through various innovations, injection molding has become one of the most efficient ways to create molded rubber products in many cases particularly with more complex shapes.
The operation of an injection molding machine requires: feeding, mixing, and injection of a measured volume of compound, at a temperature close to the vulcanization temperature, into a closed and heated mold; a curing period; demolding; and, if necessary, mold cleaning and/or metal insertion (Overmolding process), before the cycle starts again. For maximum efficiency, as many of these elements as possible should be automated.
Injection Molding Process Steps
- The uncured rubber is fed into the machine in the form of a continuous strip.
- The uncured rubber is worked and warmed by the rotation of the screw in a temperature controlled barrel.
- As the rubber stock accumulates in the front of the screw, the screw is forced backwards. When the screw has moved back to a specific point, this indicates the correct amount of rubber (shot amount) is ready for injection.
- With the mold held closed under hydraulic pressure, the screw is pushed forward. This forces the rubber into the mold (this is the injection process).
- While the rubber cures (vulcanizes) in the heated mold, the screw starts rotating and filling with the new rubber (the next shot).
- The mold then opens and the part can be removed. The machine is ready to make the next shot as soon as the mold closes again.
5. How our Auditors Check this Process in the Factory
Our engineers report back on detailed checklists that are organized in 21 sections:
- Production Capacity
- Technical Capability
- Process Controls
- QC & Inspection capabilities
- Setup Procedures
- Process Parameters
- Rubber Injection Mold Process Parameters
- Cycling Parameters
- Compression Mold Process Parameters
- Transfer Mold Process Parameters
- Silicone Rubber Extrusion
- Liquid Injection Molded Silicone (LIM), Liquid Silicone Rubber (LSR) Molding
- Two Shot Molding also known as Overmolding
- Preventative Maintenance
- Preventative Maintenance effectiveness
- Material Control
- Rubber Delivery
- Material Processing
- Tool/Die Storage
- Tool Design & manufacturing Capabilities
- Housekeeping
Did we forget something important?
No comments:
Post a Comment